If you’ve ever wondered, “why is there water filter on a compresser line,” you’re not alone. The presence of a water filter in compressed air systems may seem trivial, but it’s an essential component that plays a significant role in maintaining efficiency and prolonging the life of your equipment.
Whether you’re managing an industrial air compressor or a smaller setup, understanding the purpose and benefits of having a water filter on your compressor line can save you time, money, and frustration.
In this article, we’ll explore why this seemingly minor element is so vital, diving deep into its importance, functionality, and how it enhances the overall performance of your air compressor system.
The Role of a Water Filter on a Compressor Line
Air compressors are widely used across various industries, from automotive workshops to large-scale manufacturing plants. However, the compressed air produced is often accompanied by moisture, dust, and other contaminants. These impurities can cause significant damage if they enter your air tools or machinery. This is where a water filter becomes essential.
Why a Water Filter is Necessary
Moisture and contaminants can corrode metal parts, damage seals, and even lead to machinery breakdowns. By placing a water filter on the compressor line, you effectively remove these harmful elements, ensuring clean, dry air reaches your equipment. This results in:
- Extended Equipment Life: By filtering out moisture and particulates, you prevent rust and corrosion, which prolongs the life of your tools and machinery.
- Enhanced Performance: Clean air means your equipment runs smoother, reducing wear and tear while maintaining consistent performance.
- Reduced Maintenance Costs: Fewer breakdowns mean less downtime and lower repair costs, saving you both time and money in the long run.
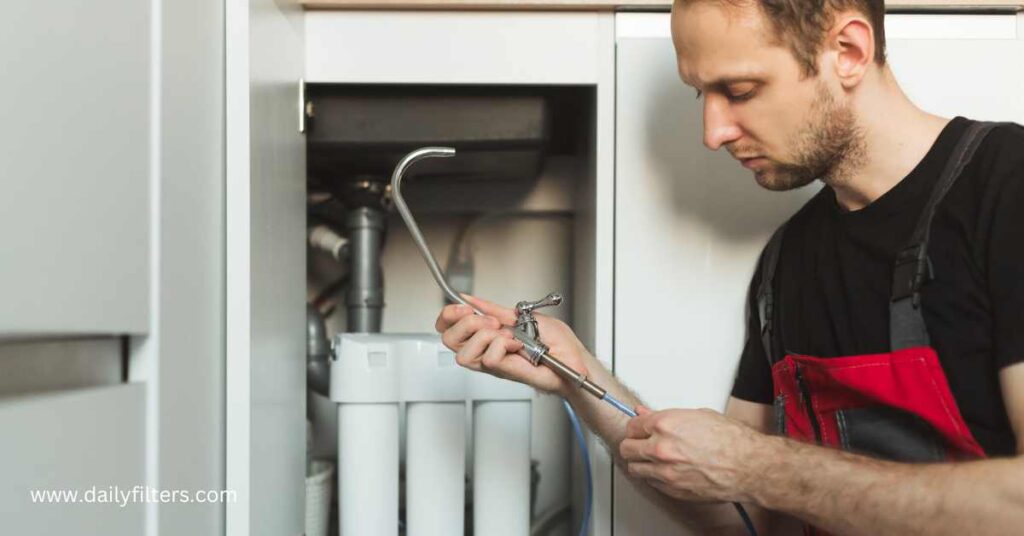
How Does a Water Filter Work on a Compressor Line?
A water filter works by separating moisture and contaminants from the compressed air before it reaches your tools. The process involves several steps:
The Separation Process
- Initial Compression: When air is compressed, moisture condenses and forms water droplets.
- Filtration: The water filter traps these droplets and other contaminants, allowing only clean, dry air to pass through.
- Drainage: Most filters come with an automatic or manual drain that removes the collected moisture and debris, ensuring the filter continues to operate efficiently.
Types of Water Filters for Compressor Lines
There are different types of water filters, each designed to meet specific needs:
- Coalescing Filters: These filters are designed to remove liquid water and oil from the compressed air, along with solid particles.
- Particulate Filters: These focus on removing dust and dirt particles from the air, protecting sensitive equipment.
- Activated Carbon Filters: Ideal for removing odors, vapors, and oil mist, ensuring air quality is maintained in sensitive environments.
Benefits of Installing a Water Filter on Your Compressor Line
Understanding the advantages of having a water filter on your compressor line will help you appreciate its importance even more.
Prevents Corrosion and Rust
One of the primary reasons to have a water filter on your compressor line is to prevent rust and corrosion. Moisture can wreak havoc on your system, corroding internal parts and reducing the lifespan of your tools and machinery. A water filter removes this moisture, keeping your equipment safe.
Improves Air Quality
Contaminants like dust, oil, and other particulates can degrade the quality of compressed air. In applications where clean air is crucial, such as in painting or food processing, a water filter ensures that the air remains pure and free from impurities.
Increases Efficiency
When moisture and contaminants are removed from the air, your compressor operates more efficiently. Clean, dry air allows for smoother operation, reducing energy consumption and wear on components. This efficiency translates into lower operational costs and better performance.
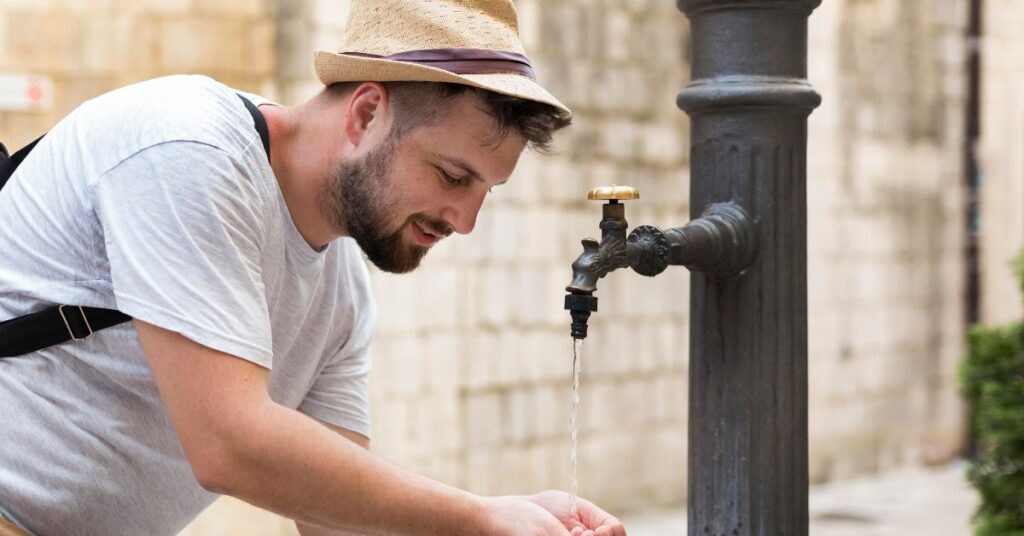
Common Issues Without a Water Filter
Neglecting to install a water filter on your compressor line can lead to several problems, including:
- Frequent Equipment Failures: Moisture and debris can cause internal damage, leading to unexpected breakdowns and costly repairs.
- Decreased Productivity: Equipment downtime due to contamination issues can halt operations, leading to reduced productivity and missed deadlines.
- Increased Maintenance Needs: Regular maintenance and cleaning become more frequent, as unfiltered air can cause premature wear on components.
How to Choose the Right Water Filter for Your Compressor Line
Selecting the right water filter depends on your specific needs and the type of equipment you’re using.
Consider Your Application
Different industries have varying requirements when it comes to air quality. For instance:
- Industrial Applications: Coalescing filters are essential for removing water and oil mist, and protecting heavy-duty machinery.
- Painting and Coating: Activated carbon filters ensure air purity, preventing imperfections in paint finishes.
- General Use: Particulate filters are suitable for basic operations, offering adequate protection against dust and debris.
Determine the Filter Capacity
The filter’s capacity should match the airflow of your compressor. Choosing a filter with insufficient capacity can lead to inefficiency, while an oversized filter may be an unnecessary expense.
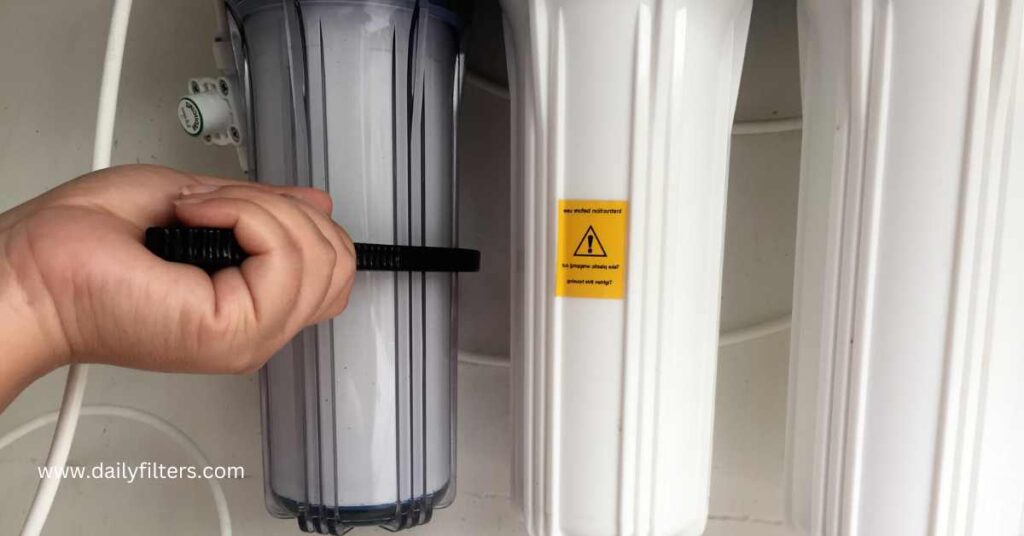
Maintenance Requirements
Some filters require frequent manual draining and maintenance, while others have automated systems that handle this for you. Consider your workload and maintenance capabilities when selecting a filter.
FAQs About Water Filters on Compressor Lines
Can I use my compressor without a water filter?
While it’s possible, running a compressor without a water filter is risky. Unfiltered air can damage your tools and machinery, leading to costly repairs and reduced equipment life.
How often should I change the water filter on my compressor line?
The frequency of changing your filter depends on your usage and environment. Typically, filters should be replaced every 6 to 12 months or when you notice a drop in performance.
What happens if my water filter clogs?
A clogged filter can cause pressure drops and reduce airflow, affecting the efficiency of your equipment. Regular maintenance and timely filter replacements can prevent this issue.
Are there different filters for oil and water?
Yes, there are specific filters designed for oil and water separation. Coalescing filters are commonly used for oil and water, while particulate filters handle solid contaminants.
Conclusion
Understanding “why there is a water filter on a compressor line” is essential for anyone using compressed air systems. These filters play a critical role in maintaining clean, dry air, which protects your equipment, enhances performance, and reduces operational costs.
By investing in the right water filter and ensuring proper maintenance, you can significantly extend the lifespan of your compressor system and ensure it operates efficiently for years to come.